With COVID-19 dominating the news one cannot help but think of the precautions and warnings about how the disease spreads. The CDC officially states that the virus can be spread mainly from person-to-person between people who are in close contact with each other (within six feet). Transmission can be through respiratory droplets, aerosol fine particles or physical contact. Depending on the geographic area of the country in which you live, the population density of your city and how frequently you encounter others, you’re susceptibility to the disease varies. As states reopen their respective economies, sensational headlines still dominate and proclaim the horrors of being in close proximity and how it’s affecting spikes in confirmed cases. 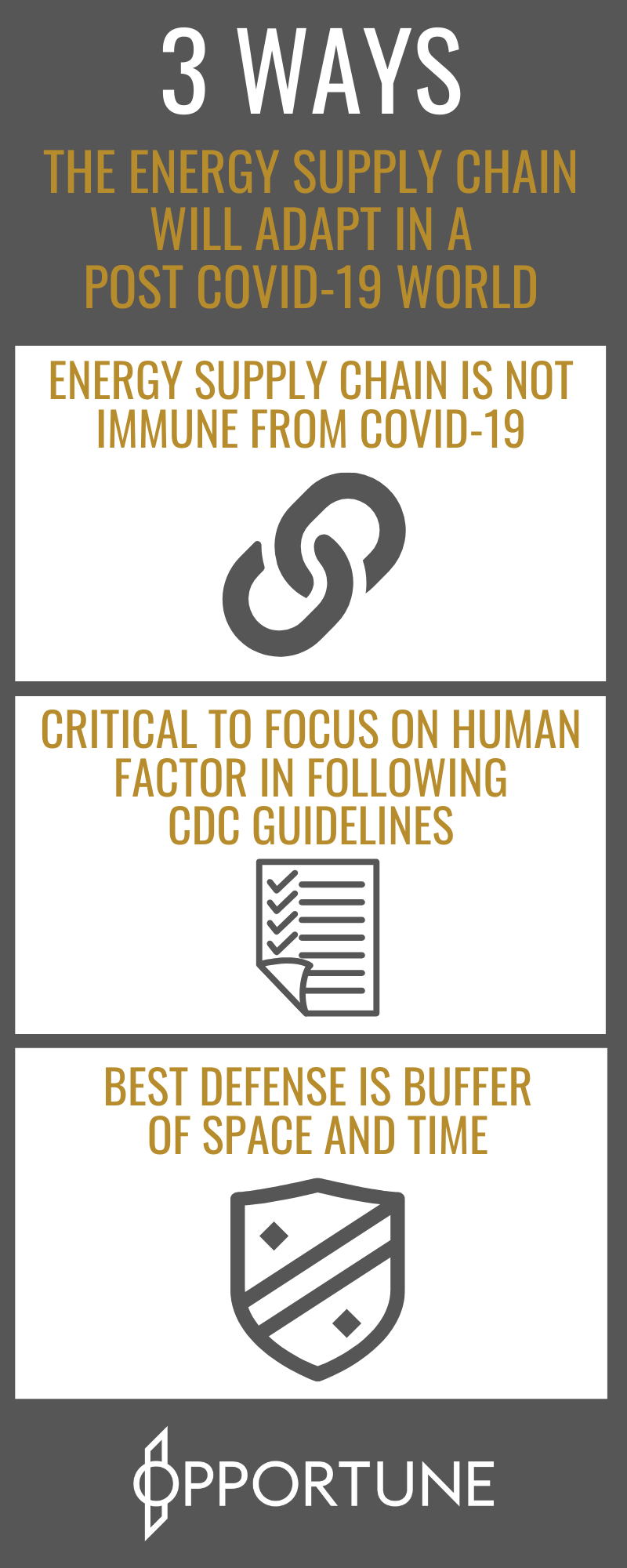
While there are less cases in rural areas, worry and angst remains prevalent as the spread of COVID-19 persists. To reopen, the CDC publishes countless pages extolling the virtues of cleaning and disinfecting, how to maintain a healthy work environment and who should get tested.
What does this all mean? I think that the one common theme here is that no one knows for certain about what the right way in which society can and should return to “normal”. No one knows exactly how close people can be and still be safe. No one is clear on how quickly we can return to pre-COVID life.
COVID-19: Impact on the Supply Chain
Unfortunately, what permeates the airwaves and headlines in our personal lives carries over into the supply chain as well. The same guidelines for social distancing in restaurants and retail also ripple out to the energy industry. Of course, these stories don’t make headlines until there’s an issue. It’s only in extreme cases where the supply chain makes the news.
Take for example recent news about the meat packing industry. When we go to the grocery store, there isn’t a second thought on how the meat is packaged and prepared. We’re only concerned that we’re the only one at the counter, no one else is within six feet and that everyone (hopefully) is wearing masks. Recent headlines are reminders of the working conditions and tightly packed assembly lines that employees endure at meat packing factories.
How will the energy supply chain deal with the new normal? When you fill up your car with gasoline, you don’t think of all the touchpoints and the journey of the barrel of oil to a refinery, production of gasoline and distribution to your gas station. You shouldn’t have to. Instead, you think about the price of gas when filling up your car or truck. How can the energy supply chain avoid staying out of the headlines with massive disruptions? There isn’t going to be an easy answer. There’s no magic bullet to solve all aspects equally. What works for one part of the energy industry will not work for others.
Optimization: Human Factor
Supply chain optimization focuses on connectedness and removing boundaries and barriers to moving product from Point A to Point Z, with all points in between. Over the years, the focus has been for increased automation and digitization. Even so, there’s still a tremendous reliance on the human factor. Systems can automate connections on the paper side of the supply chain and tracking.
"Our new supply chain will have to be a disconnected connectedness—that is, small buffer zones and boundaries may be required to protect the human involvement."
However, the physical logistics aspects still involve humans and human interaction. Men and women still drive the trucks and operator trains. Men and women still work with the pipeline and terminals. Vessels have human crews onboard that accompany crude or refined products. So, even with all the digitization and automation occurring, “touchpoints” and interactions between people remain critical parts of the energy supply chain interface.
In the context of social distancing and minimizing human contact, what will the “new normal” look like? Let’s take the CDC measures at face value and apply those to a “new world” for moving energy.
First, the CDC recommends that hands be washed often and using a hand sanitizer that contains at least 60% alcohol. The CDC’s guidelines suggest avoiding touching the eyes, nose and mouth with unwashed hands. For the energy industry, this one will vary for ease of compliance. Workers, using gloves, will be regularly handling equipment (i.e., pipes, valves, gauges, instrumentation, hoses, etc.). Depending on their location, they may have access to hand-washing stations. More likely than not in remote areas, hand-washing stations will be limited. This translates into an added cost for substitutes like hand sanitizers, extra gloves and other PPE (personal protective equipment) protection.
Second, the CDC guidelines stipulate that you should avoid being in close contact with those who are sick. It’s easy to avoid someone when that person has obvious symptoms. However, cases of COVID-19 have been found in individuals who are asymptomatic, meaning those that may not outwardly show symptoms, but the virus may be present mutating in the body. A recent study out of the University of Virginia illustrated that people who eventually experience symptoms of COVID-19 don’t always present symptoms immediately. So, this one will be more difficult, especially when crews need to be in close proximity working. This becomes especially difficult for workplaces like those on ocean-going vessels or workers on offshore rigs.
Third, the CDC says that you should cover your mouth or nose with a cloth face cover when around others. This may be easy enough in a normal office setting. However, for those in the field, vocal communication is essential. A face covering could limit the effectiveness of vocal communication when worn with other PPE. It’s not enough to have just one mask. Masks, like other articles of clothing, get dirty and must have their filters routinely changed. The right mask must serve a role to protect a worker yet allow proper communication.
What Does This All Mean?
There’s no easy answer for how the energy supply chain could easily adopt the CDC guidelines for mitigating the spread of COVID-19 in all cases with 100% effectiveness. The energy industry naturally was borne out of the habit of relying on human interactions and the transference of products from one person to another.
As crude oil is extracted out of the ground by human crews, it’s then transported to a pumping or rail station by other individuals. While in-transit, there could be limited human interaction. However, again, individuals are required to connect hoses, open or close valves or use other equipment once products get to their destination. After leaving a refinery, humans must load a vessel, exchange paperwork, use equipment or interact with other instrumentation to keep the product moving. Jobbers use hoses and tools to open compartments to load and unload trucks.
"Above all, companies will need to reassess their buffer zones of human interaction to ensure that proper health and safety measures are routinely applied to stave off further spread of COVID-19 within the human workforce."
Our new supply chain will have to be a disconnected connectedness—that is, small buffer zones and boundaries may be required to protect the human involvement. When a human interacts with tools, machinery or other equipment, the buffer and disconnectedness will be additional PPE. When other humans are involved, the buffer will be space in the form of “social distancing” as recommended by the CDC and other health organizations (as much as can be allowed).
In the end, the biggest buffer will be increased time. Time is required to adhere to new guidelines. Time is required to make sure that surfaces are clean, instrumentation is cleaned after use and proper guidelines are being properly followed for these interfaces. Time is required for staggering crews and allowing for recovery from those feeling COVID-19 symptoms.
Ultimately, the goal is to mitigate any supply chain disruptions as feasibly possible, while adhering to CDC guidelines with respect to fending off transmittal of COVID-19. Early in the crisis, China shut down shipyards completely, stranding work that was being done to vessels. China is now only starting to reopen to state-owned shipyards, but private shipyards remain closed. Domestically, the shutdowns globally for COVID-19 have snarled the supply chain. Companies that diversified globally are faced with shortages of critical parts made overseas. While these headlines may not affect consumers directly, a COVID-19 impact at a fuel terminal or to pipeline operations could disrupt the flow of product to end-customers.
Therefore, the “new normal” will indeed be different, not only in the energy industry, but in supply chains across a host of industries. No longer will there be a sole focus on driving out costs and increasing overall throughput. New technologies and process adaptations will now be required for companies to remain competitive. Above all, companies will need to reassess their buffer zones of human interaction to ensure that proper health and safety measures are routinely applied to stave off further spread of COVID-19 within the human workforce.